Case Studies
Dr Pepper Manufacturing Plant
TEAM
ORS Multidisciplinary Team
Sector
Services Provided
Fire Safety, PSDP and Assigned Certifier
Overview of service
This world-class manufacturing plant will act as an international operations hub for soft drinks maker Keurig Dr Pepper. Located in Newbridge, Co. Kildare, the warehouse building is 300,000 sq. ft. on a site of approximately 7.42 ha.
Alder Glover Limited appointed ORS as the lead design team to provide Fire, Disability Access, PSDP and Assigned Certifier services for the development.
The application scheme is for a 7-year permission to facilitate the change of use of a permitted warehouse distribution centre to a beverage manufacturing facility and ancillary works to be delivered in two phases. The application also includes an element of retention to regularise additional office and warehouse floor areas beyond those areas previously permitted.
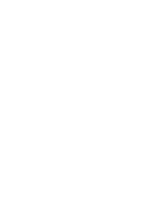
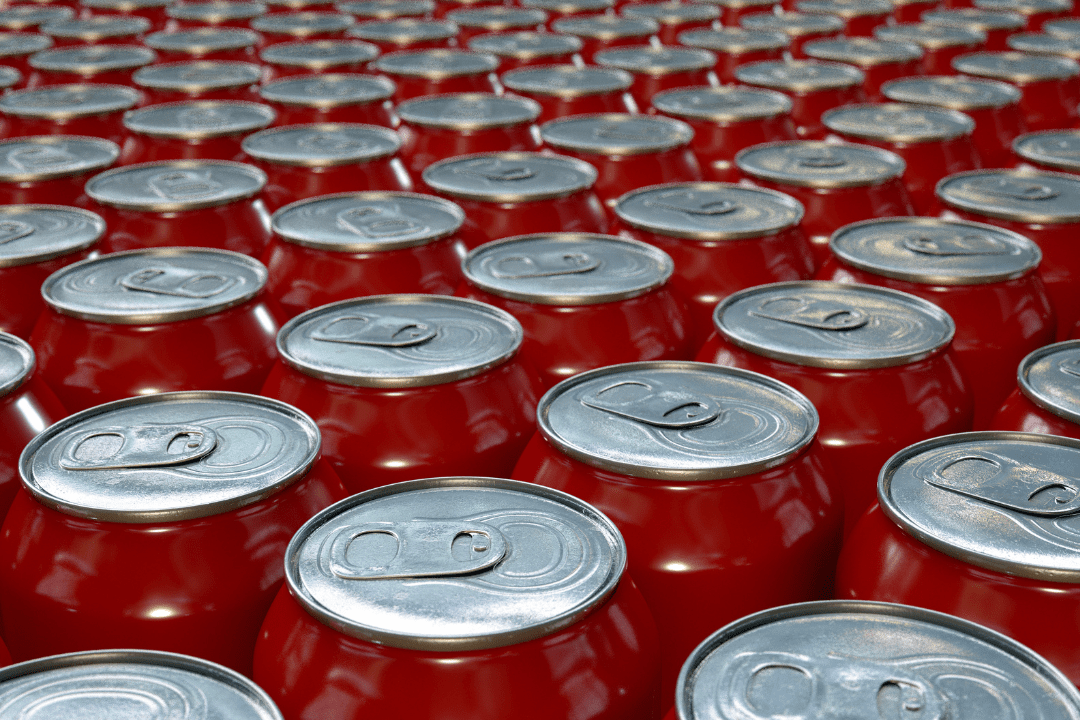
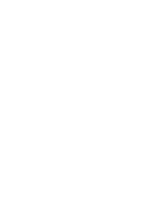
In summary, the proposed development comprises of:
- Conversion of the warehouse building into a production and warehouse facility to produce beverage concentrate.
- Construction of barriers at the southwest and southeast corners of the site.
- Construction of a tank farm and pipe bridge infrastructure for the storage and transportation of raw materials.
- Construction of a new wastewater treatment facility.
- New fire water retention pond.
- New perimeter security fence; and
- Provision of all ancillary development works, above and below ground
The project is an excellent example of how the firm delivers complex multidisciplinary solutions by taking an efficient and simple approach for the client. This involves appointing a project coordinator as a single point of contact for the client.
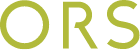
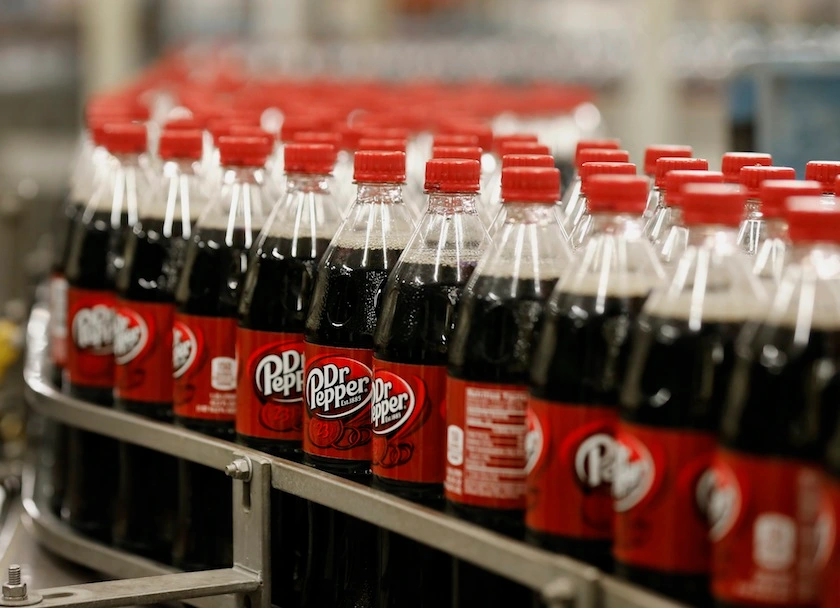
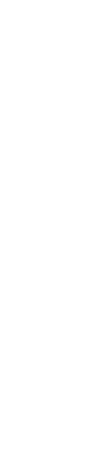
Project challenges
A phased approach to certification
Getting the project up and running for the client to start manufacturing was a priority. Prior to completion, the ORS Fire Safety Team carried out their final inspections.
The production area was ready for completion, while the ancillary services were not. ORS discussed this challenge with the client and suggested a phased strategy solution. With this approach, ORS introduced two separate completions. The team split the fire sign-off to allow manufacturing to commence. This was also discussed and agreed upon with Building Control. As a result, manufacturing could commence under the BCAR fire safety sign-off of phase 1.
During this new phased approach, a challenge was ensuring that life safety services were fully operational and offering complete cover to the now-finished manufacturing/production area. In the construction zone, however, life safety services needed to remain zoned and/or isolated for the purposes of undertaking specific works. To ensure life safety was never compromised, a temporary solution was utilised to provide cover throughout the construction zone at all times until work was complete and the system went live. Another challenge with continuing construction works within a live environment was ensuring an accessible escape route was maintained through the live construction site. This was successfully managed and executed as a result of appropriate planning and strong communication between all parties.
An innovative approach that came to light on this project was that a production line conveyor belt traversed directly through a compartment line in the manufacturing area. With some clever engineering, a solution was developed in which, on activation of the fire alarm, a slight timed delay was programmed for the engagement of the fire curtain to allow the conveyor belt to mechanically separate and move out of the compartment line. Once complete, the fire curtain would then fully engage, creating the required fire line compartment.
Related Projects
Talk to A specialist