A complete guide to emergency lighting
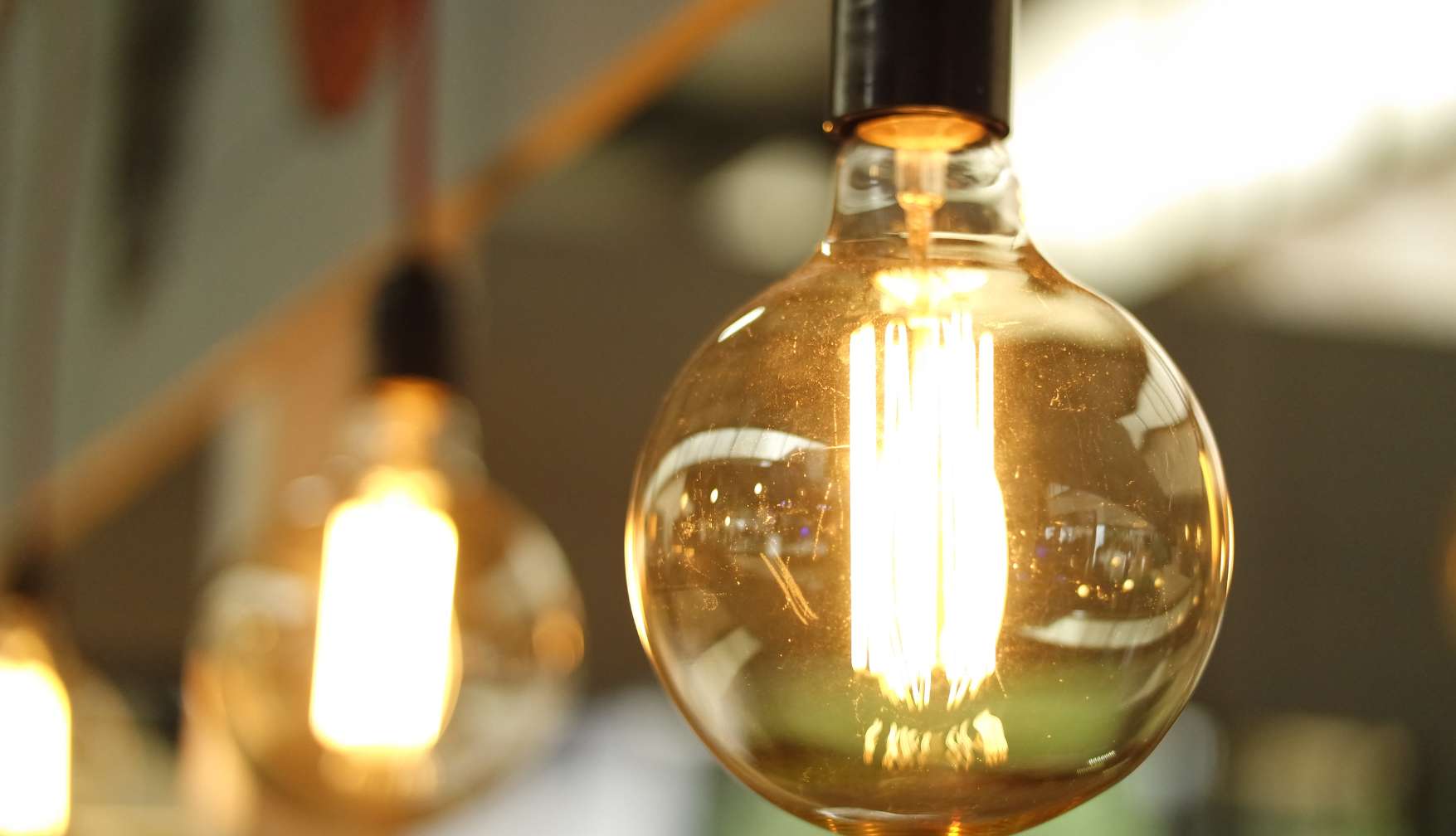
In the event of an emergency, emergency lighting is the first line of escape. This is part of an active fire prevention system and is installed throughout all building types as part of the safety provisions of a building.
The emergency lighting system is an integral part of the overall design of a building to reduce anxiety and stress should a power failure take place. In the event of a fire when the electrical power supply may be compromised, the evacuation of occupants is challenging. The provision of emergency lighting provides comfort and visual capabilities for safe and effective evacuation through escape routes.
It helps to identify fire alarm panels, call points, firefighting, safety equipment, exit points and hazards such as stairs, changes of direction, intersections, slopes. If the immediate area outside the final exit has hazards in darkness, risk assessment should determine if further emergency lighting is needed until safety can be reached.
Emergency escape lighting is not designed to allow normal operations to be continued in the building in the event of failure of the normal lighting. Standby lighting is used for areas where normal activities are required to continue substantially unchanged in the event the supply to the normal lighting fails.
Emergency lighting systems must be installed by a competent person accredited by a professional body.
There are three modes of operation of emergency lighting;
- Non-maintained – where the emergency lamps are not energised until there is a mains failure.
- Maintained – where the emergency lamps are energised at all times.
- Sustained – where an emergency luminaire has two or more lamps, at least one of which is operated from the emergency supply, and the remaining are from the normal mains supply.
There are two main categories of emergency lighting systems; those powered from a central source and those with a local source (self-contained system), and the limitations and advantages of each type should be considered before any decision is made about the type of system required.
Central battery system:
A central battery system is a system where an electrical supply is distributed to luminaires from a central battery source in the event of a power failure. The source is normally kept in a charged state by a charger and control equipment. Central battery systems are the most cost-efficient in medium or large installations or where central or control testing is required.
The advantages of the system are;
- The batteries can last up to 25 years if properly maintained
- Testing and maintenance are easier and less expensive
- Slave luminaires are less affected by local temperature variations
- This type of system is more cost-effective on larger installations
The limitations of the system are that the battery storage area requires a separated, well-ventilated compartment, and all cabling must be of fire-resistant material. Systems require more monitoring and subcircuit protection devices.
Self-contained system:
In a self-contained system, the luminaires contain all the elements such as the battery, lamp, control unit and monitoring facilities within the unit or located within a 1metre distance from the unit. When power failure occurs, the luminaire will operate automatically from the battery power source. Following partial or complete discharge, the battery will be recharged on resumption of the normal power supply.
The advantages of this type of system are:
- There is no routine battery maintenance required
- As each device contains its backup supply, there is no requirement of separate sub-circuit protection or monitoring
- The system is easily extendable as no special wiring is required
- For smaller installations, the system may be more cost-effective
- Fail-safe operation guaranteed as the backup power source is present at the location
The limitations of a self-contained system are that batteries generally require replacement between three to five years, and this can be an onerous and expensive task in large installations. These devices are more costly than slave luminaires, and the battery working temperatures limit operating temperatures.
The requirement to provide emergency lighting systems is enshrined in various pieces of legislation:
- The Fire Services Act 1981-2003
- Health, Safety and Welfare at Work Act 2005
- Building Regulations (TGD: B) 1997-2020
The National Standard for designing and installing emergency lighting systems is IS 3218: 2013 + A1: 2019 and is the minimum requirement for design purposes. Within this code, reference is made to a number of normative standards which must also be complied with.
All building owners are required by law to ensure emergency lighting on their premises is fit for purpose, maintained, and tested on a regular basis.
For escape routes up to 2 m in width, the horizontal illuminance on the floor along the centre line of an escape route should not be less than 1 lux, and the central band consisting of not less than half of the width of the route shall be illuminated to a minimum of 50 % of that value as shown in Figure 2 IS 3218: 2013 + A1 : 2019.
- Defined escape routes up to 2 metres in width:
- 1 lux minimum along the centre band
- Half-width of corridor shall be 0.5 lux.
- Wide escape routes
- Treated as a series of 2 metres wide corridors.
- Treated as open area lighting with 0.5 lux throughout
- Undefined escape routes/open areas (anti-panic) lighting
- Open area are larger than 60m2 floor area or smaller areas if there is additional hazards such as the use by a large number of people.
Emergency Lighting for escape routes, including external ones, must have sufficient lighting for people to see their way out safely. Emergency escape lighting may be needed if areas of the workplace are without natural daylight or are used at night. Emergency lighting needs to function not only on the complete failure of the normal lighting but also on a localised failure if that would present a hazard. Emergency escape lighting should:
- Indicate the escape routes clearly;
- Provide illumination along escape routes to allow safe movement towards the final exits; and
- Ensure that fire alarm call points and firefighting equipment can be readily located.
In addition to emergency escape lighting, it may be necessary to provide other forms of emergency lighting for safety reasons, for example, to ensure that manufacturing processes can be shut down safely.
Emergency lighting units should be installed in the following areas:
- At each exit door.
- Near each staircase so that each flight of stairs receives direct light.
- Close to any change in floor level.
- Outside each final exit.
- By exit and other safety signs that are required.
- Within lift cars.
- Near firefighting equipment.
- Near each fire alarm call point.
- Toilet facilities. Disabled toilets. Toilet lobbies.
- In all motor generator rooms, control rooms, switch rooms, plant rooms and adjacent to main control equipment associated with the provision of normal and emergency lighting to the building.
- Refuge areas.
- External roof-mounted plant or roof plant rooms for buildings that have external roof-mounted plant or roof plant rooms that require regular access (e.g., for maintenance).
The lighting units should be placed as low as possible but at least 2 metres above floor level (measured to the underside of the lighting unit). The units should be erected in locations that will limit the risk of smoke accumulation, making the lighting ineffective.
Emergency escape lighting should be located on the premises where staff and members of the public have access. These routes would normally include stairways, corridors and exit doors. This should also include locations containing firefighting equipment such as fire extinguishers, hose reels and safety and security equipment such as key box holding emergency keys to exit doors.
Where possible, the height of individual luminaries should be located at least 2m above floor level, where this is not possible, a risk-assessement approach should be taken. Any windowless toilet facility exceeding a floor area of 8m2 is required to be fitted with emergency lighting. All disabled toilets are required to be fitted with emergency lighting.
The proper maintenance and testing of emergency equipment are important so as to ensure an effective operating system is in place in the event of an emergency. The system needs to be maintained in accordance with the provisions of IS 3218: 2013 + A1: 2019 and will comprise of the following;
- Daily in-house inspections to include visual inspection of healthy indicators in a central battery system. Any system faults logs are given urgent attention and recording of the corrective actions taken.
- Weekly in-house inspections to include every LED indicator being checked is operating effectively. The logbook should be checked to confirm rectification of any previously recorded faults logged, and the logbook should be updated to the findings of the weekly check.
- Quarterly inspections to be completed in-house by a competent person to include checking of logbook compliance. Every emergency luminaire and emergency exit sign to be energised from its internal battery source for a period of 30 minutes, and on completion of the test, each LED indicator to be checked to be correctly illuminated.
- A competent person must complete an annual inspection to include logbook compliance, and every luminaire to be energised from its internal battery source for three hours. During that period of time, a visual inspection of each luminaire is needed to ensure they are functioning properly. On completion of the test, all LED indicators to be checked for proper functioning.
- Testing every four years is required to check the illumination levels provided by the emergency lighting system.
If you would like to discuss Fire Safety requirements for your project, please get in touch with Rory Walsh from the ORS Fire Safety Team.