Can Lean practices and BIM change how we deliver public buildings in Ireland?
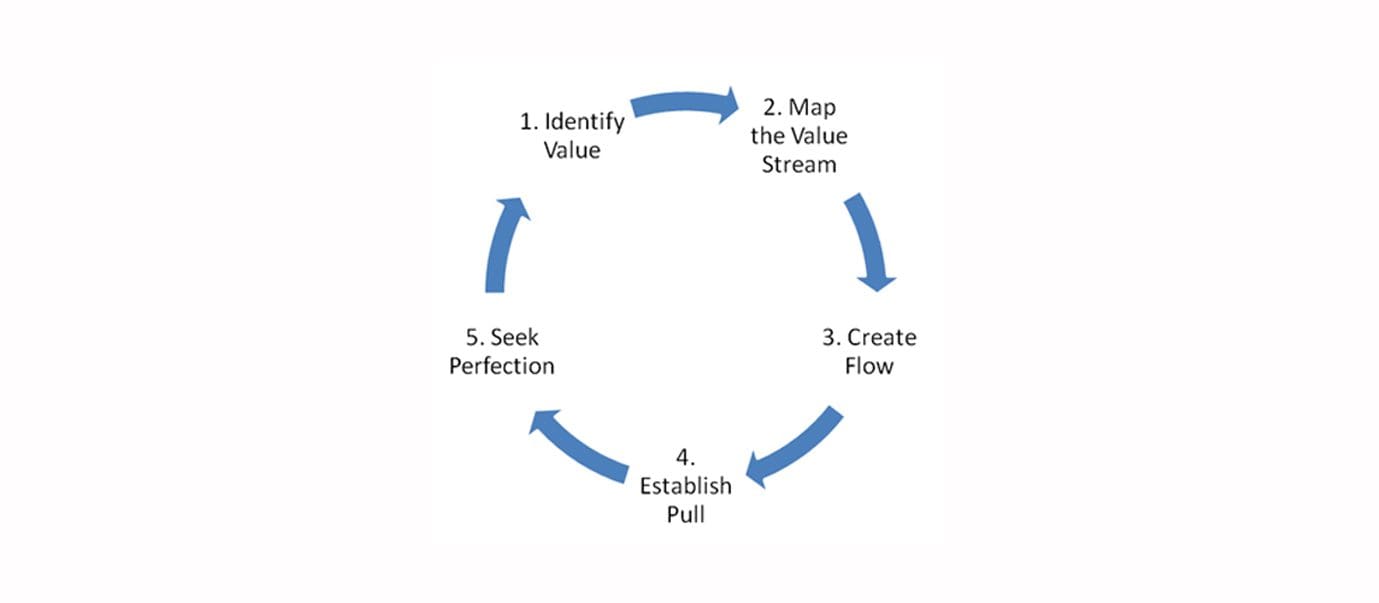
Can Lean practices and BIM change how we deliver public buildings in Ireland?
In recent years, two major developments have imposed a disruptive change in the Architectural, Engineering and Construction (AEC) industry. First is a streamlined approach to project and construction management— Lean Construction principles — and second is an adaptive information technology — Building Information Modelling (BIM) ) (Sacks, Koskela, Dave, & Owen, 2010). In 2017 the National BIM Council in Ireland acknowledged how the strategic use of BIM can support a leaner more innovative construction sector thus addressing declining productivity prevalent in construction.
Lean principles are being led by a group of early adopters in Ireland, where large multinationals operating in the country required an integrated Lean and BIM approach to design and construction. The recently established Irish chapter of the Lean Construction Institute is looking to transform design and delivery on construction projects by passing Lean techniques to the industry as this can provide the foundation for a more collaborative and effective form of project management (Lehane, 2014). The principles of Lean Construction are illustrated in Figure 1.1.

Figure 1.1 – Principles of Lean. (Lean Enterprise Institute, 2000)
Lean Best Practice for Construction and Integration of BIM
Lean construction and BIM are not only synergistic as the associated benefits span from project conception to demolition (Sacks et al. 2010). Sacks (2010) found that three Lean principles had the most interactions with BIM:
- Reduction of waste by getting the quality right first time by reducing product variability;
- Improved flow and reduced production uncertainty;
- Reduction in overall construction time.
This synergy has been strengthened in recent years with the rapid advent of multidimensional BIM capabilities. These interactions were examined further by Dave et al. where the implementation of Lean and BIM was placed in focus. The primary benefits of adopting this dual approach are illustrated in Figure 1.2.

Figure 1.2 – Benefits of using Lean and BIM. Adapted from “Implementing Lean in Construction: Lean Construction and BIM” by Dave et al., 2013, Figure 1.5, p. 7, Copyright 2013 by CIRIA.
The output of linking the project plan to 3D BIM to create a simulation of the construction activities over a defined period is called 4D BIM (Fosse, 2015). Through this exercise the design and construction teams can gain a deeper understanding of all components required to complete the commission when compared to working with 2D drawings. If used appropriately, 4D scheduling can also serve the function of a virtual ‘first run study’ (Fosse, 2015) and can improve flow and reduce production uncertainty.

Figure 1.3 – Lean and BIM Workflow – functions. Adapted from “Implementing Lean in Construction: Lean Construction and BIM” by Dave et al., 2013, Figure 2.1, p. 10, Copyright 2013 by CIRIA.
The primary function of Lean and BIM during the construction stage is to minimise waste and shield production from uncertainty. When these functions combine effectively the outcome is a reduction in the construction programme and improved quality (and value) for the client (Dave et al., 2013).
Procurement, Lean and BIM
The incorporation of an Integrated Project Delivery (IPD) form of contract with Lean Construction principles and BIM has potential to enrich the design and construction process.
This collaborative style of project delivery has been rigorously tested in the USA by Sutter Health throughout their $5.5 billion development of new acute and non-acute care facilities, medical centres, office buildings and significant remodels of existing structures to ensure that they comply with the seismic design requirements in California (Lichtig, 2005). Sutter Health required their design and construction teams to adopt Lean Construction principles and instilled 5 Big Ideas as the framework for approaching all aspects of their Lean Project Delivery (Lichtig, 2005) as follows:
- Collaboration;
- Increase relatedness among all project participants;
- Optimise the project not the piece;
- Tightly couple learning with action;
- Projects are networks of commitments.
Having an IPD contract in place incentivised driving the cost below the target design value (Yoders, 2010). This approach ensured savings across each project stage. For the Cathedral Hill project, savings were derived from planning the co-located mechanical, electrical, plumbing and structural works.
Test Case for BIM & Lean Integration
The importance of BIM and Lean has been recognised by many by bringing together technology, process improvements and digital information “to radically improve project outcomes and asset operations” (Construction Industry Federation, 2017). This paradigm was tested by CitA and the RIAI in 2012 when the BIM community in Ireland were looking for pilot projects to demonstrate the power of collaborative work practices, 3D modelling and Lean principles in practice (McAuley, Hore, O’Loingsigh, & Deeney, 2014). After consultation with the Department of Education and Skills, a Generic Repeat Design (GRD) Primary School was selected as a trial project. The consultants involved in this study co-located and created discipline specific parametric models that were subsequently federated for the purposes of clash detection, construction sequencing and cost analysis (McAuley et al., 2014). The results of this practical study strongly advocated the application of BIM to become mandatory in future public works projects. The BIM model tested eventualities that could potentially occur on site and subsequently aided in avoiding potential problems, in the test case, as the building was virtually built which allowed foresight on a number of key areas (McAuley et al., 2014).
This approach has been justified in recent years where BIM has been mandated by Government bodies on a number of high profile public projects that are currently under construction and are realising some of the benefits outlined above.
Conclusion
In addition to the integration of BIM tools to reduce waste, the adoption of Lean Construction principles with Integrated Project Delivery (IPD) has potential to enhance overall project delivery on public projects. In the last decade, the procurement model has tilted towards IPD to assist project teams in achieving Lean Construction at a time when the industry is searching for ways to eliminate waste, cut costs, improve productivity, and create positive outcome (Carbasho, 2008).
The importance of BIM and Lean has been recognised by many by bringing together technology, process improvements and digital information “to radically improve project outcomes and asset operations” (Construction Industry Federation, 2017). The Irish Government also recognise that the creation of virtual assets can be leveraged to improve estate and facilities management practices (National BIM Council, 2017).
It is apparent that the adoption of Lean best practice for construction and integration of BIM on public sector projects can support a more innovative AEC industry and can potentially address declining productivity prevalent in construction (National BIM Council, 2017).
ORS Expertise
ORS Civil and Structural Team employs Lean project management techniques to their design activities and have tapped into the synergies associated with pairing this with BIM on projects. Contact a member of our team today for information on how this could benefit your project.
References
Dave, B., Koskela, L., Kiviniemi, A., Tzortzopoulos, P., & Owen, R. (2013). Implementing Lean in Construction: Lean construction and BIM. CIRIA Lean Series.
BIM Ireland. (2016, May 4). JJ Rhatigan & Company – Leading the Way in BIM and Construction Technology. Retrieved 6 May 2017, from http://www.bimireland.ie/2016/05/04/jj-rhatigan-company-leading-the-way-in-bim-and-construction-technology/
Carbasho. (2008, July 15). Integrated Project Delivery Improves Efficiency, Streamlines Construction. Retrieved 25 November 2017, from https://www.tradelineinc.com/reports/2008-7/integrated-project-delivery-improves-efficiency-streamlines-construction
Construction Industry Federation. (2017, December 13). A Digital Strategy for Construction will Future-Proof our Industry. Retrieved 4 January 2018, from https://cif.ie/2017/12/13/digital-strategy-construction-will-future-proof-industry/
Fosse, R. (2015, February 12). How 4D scheduling creates synergies between BIM & Lean. Retrieved 6 January 2018, from http://blog.synchroltd.com/how-4d-scheduling-creates-synergies-between-bim-lean
Hore, Hunt, & McAuley. (2016). Leadership in Transition Survey Report (Survey) (pp. 1–6). Retrieved from http://www.bimireland.ie/wp-content/uploads/2016/11/EI-CitA-BIM-Ireland-2016-Survey.pdf
Lean Manufacturing Tools. (2017). Waste of Transport; causes, symptoms, examples, solutions. Retrieved 7 January 2018, from http://leanmanufacturingtools.org/101/waste-of-transport-causes-symptoms-examples-solutions/
Lehane, P. (2014, August 5). CONSTRUCTION SECTOR TILTING TOWARDS LEAN? Retrieved 4 January 2018, from http://buildingservicesnews.com/construction-sector-tilting-towards-lean/
Lichtig, W. H. (2005). Sutter Health: Developing a Contracting Model to Support Lean Project Delivery. Lean Construction Journal, 2(1). Retrieved from https://www.leanconstruction.org/media/docs/lcj/V2_N1/LCJ_05_008.pdf
McAuley, B., Hore, A., O’Loingsigh, M., & Deeney, J. (2014). Aligning BIM and Lean Methodologies within Capital Works Management Framework in Ireland. In Proceedings of the International Conference on Computing in Civil and Building Engineering. Orlando Florida. Retrieved from https://arrow.dit.ie/cgi/viewcontent.cgi?article=1061&context=beschreccon
McPartland, R. (2017, March 14). What is the Digital Plan of Work? Retrieved 19 November 2017, from https://www.thenbs.com/knowledge/what-is-the-digital-plan-of-work
National BIM Council. (2017). Roadmap to Digital Transition for Ireland’s Construction Industry 2018-2021. National BIM Council. Retrieved from http://www.cita.ie/wp-content/uploads/2017/12/NBC-Roadmap-2018-2021.pdf
Nowotarski, P., Paslawski, J., & Matyja, J. (2016). Improving Construction Processes Using Lean Management Methodologies.pdf. Elsevier Ltd. Retrieved from https://drive.google.com/file/u/0/d/1r8QWJ297wZdVVj40Wq2a8HsLNmhYqzMw/view?usp=drive_web&usp=embed_facebook
Sacks, R., Koskela, L., Dave, B. A., & Owen, R. (2010). Interaction of Lean and Building Information Modeling in Construction. Journal of Construction Engineering and Management, 136(9), 968–980. https://doi.org/10.1061/(ASCE)CO.1943-7862.0000203
Sheppard, T. (2011). Ireland’s Generic Repeat Design Schools Programme. ORGANISATION FOR ECONOMIC CO-OPERATION AND DEVELOPMENT.
Tezel, D. A. (2016, October 21). Lean and BIM Synergy in Practice – A General Overview. Retrieved 6 January 2018, from http://leanconstructionblog.com/Lean-and-BIM-Synergy-in-Practice%E2%80%93A-General-Overview.html
Yoders, J. (2010, July 10). Lean principles + Integrated Delivery = Project Savings. Retrieved 26 November 2017, from http://bimforum.org/2010/10/07/lean-principles-integrated-delivery-project-savings/