Maximise the appeal of your retail units
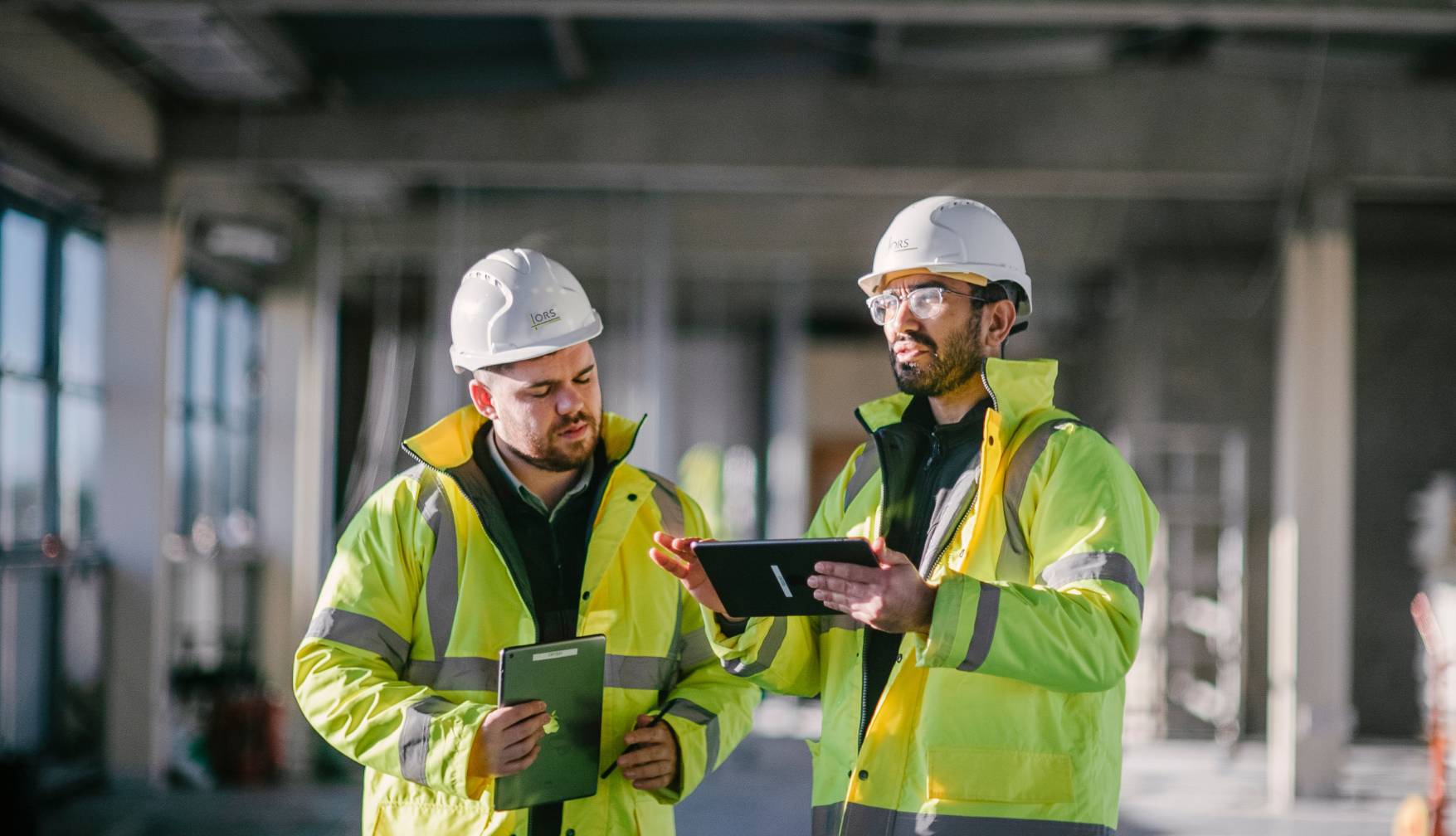
Introduction
When designing and constructing multi-storey residential or commercial buildings, ground-floor retail units are sometimes an afterthought. This is predominantly due to uses of the upper floors taking precedence from a design, financial and size point of view e.g. residential and office space.
Tenants will typically conduct feasibility reviews of several potential units at once, as they expect that a percentage won’t meet their requirements. Given ongoing market conditions and the level of inflation currently seen in the construction sector, the cost of a unit fit-out is a key criterion considered here.
For a developer to maximize the appeal of their retail unit to tenants, it is recommended that they and their design teams consider the following four criteria:
Drainage Pop-Ups
While general retailers who specialise in clothing and electronic sales would have a minimum requirement for drainage (only staff toilets, and colleague rooms), other retailers such as restaurants, coffee shops and supermarkets have a much higher drainage requirement. Supermarkets for example can require drainage pop-ups to be provided to each of their fridge cases, freezer cases and coffee stations to ensure condensation and food waste can be removed via gravity from the sales floor. This typically results in anywhere from 5 – 20 pop-ups being located throughout the front and back of the units.
While pump drainage can be used where gravity drainage cannot be accommodated, this is a last resort given the cost and ongoing maintenance required.
Incorporating a wide array of drainage pop-ups into the shell and core design can significantly increase the viability of a unit while decreasing the risk of delays and cost overruns to tenants.
It is essential that developers give consideration at the design stage to what type of tenant they are looking to attract and ensure the correct drainage is provided within the design of the unit.
Structural Loads/Floor Build Up
Given current inflation and its impact on the cost of construction materials, developers and their design teams are working to assume minimum superimposed dead loads for tenants’ floor build-ups and finishes. In addition, raised access floor systems have become an industry standard for commercial buildings given their cost, ease of installation and minimal loadings in comparison to void formers and concrete screeds.
Certain Retailers will have high floor loading requirements of 4kn point loads which translates to around 400kg (from shelving and its contents) transferred to the floor structure through shelf footings. When these loadings are added to the self-weight of the tenant’s preferred floor finishes and floor build-up, this can exceed the design loads allowed for by the shell and core’s structural engineer.
This can result in tenants having no option but to specify a lightweight or fibre-reinforced screed which are circa x8 (lightweight) or x4 (fibre-reinforced) times the cost of standard concrete screeds and not widely available in the ROI.
Deliveries
With local planning authorities pushing for the use of sustainable forms of transport to new developments (public transport, cycling and car sharing etc.) the regular deliveries of stock and goods to retail units can be easily overlooked.
Tenants will typically conduct delivery-specific site inspections and auto-track analysis on proposed delivery parking and routes during their feasibility review to ensure the following:
- The delivery vehicles’ route to the designated loading bay is sufficient and does not present risks to other road users/pedestrians.
- There is adequate space in the loading bay for the type of delivery vehicle proposed.
- The route to the unit from delivery parking has a minimal slope and short run.
Loading bays which are located on the opposite side of live roads in city centre locations present a considerable health and safety risk which tenants’ insurers will likely not cover and immediately make a unit unviable from an operations perspective.
Plant Areas
With the update of Technical Guidance Document: Part L in early 2022, retail units in newly constructed developments must ensure their energy use includes a percentage of renewables to comply (project dependent but typically 10-20%). This has resulted in dedicated tenant plant areas being required for retail units to house air conditioning units, heat pumps, solar panels and heat recovery units etc. The issues the ORS Project Management Team have noted are as follows:
- Incorrectly sized plant areas or no plant area allowed for.
- No risers from GF retail units to roof level.
- Long runs from units to plant areas, increasing the costs of pipe/ductwork.
- Incorrectly sized M&E sleeves cast during shell and core works.
- Plant areas located near acoustically sensitive units.
Conclusion
By considering the criteria outlined, you are:
- Increasing the attractiveness of your retail unit for various different tenant types.
- Reducing the design workload and therefore timelines required for a tenant to conduct their feasibility review, design and store fit-out.
- Potentially reducing any additional incentives that may have to be offered to secure a tenant.
- Ensuring that your shell and core design can result in forward planning and spend, paying dividends in the years to come.
Contact the ORS Project Management Team to learn how we can provide expert project management consultancy services for your project.