Modular Design & Construction
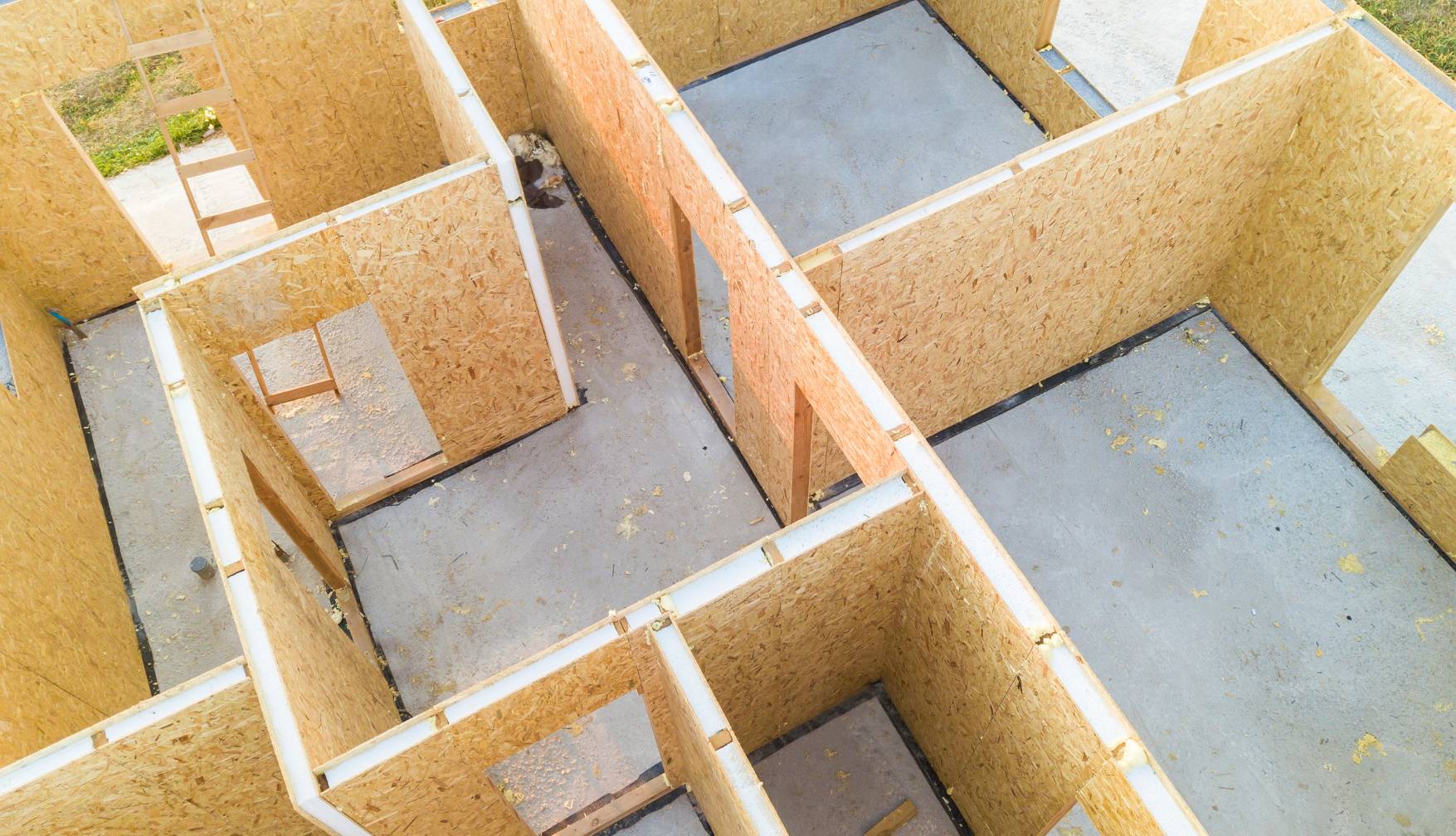
Modular construction has been in use in Ireland for decades and is now a well-established ‘modern method of construction’ (MMC) in the construction industry. Two-dimensional and three-dimensional pre-fabrication is available in all forms of construction and is favoured in cases where a large degree of repletion and modularisation can be achieved, such as multi-unit residential developments and low-rise commercial buildings. Three-dimensional fabrication includes fabrication under factory conditions of large modules, limited by maximum allowable transportation dimensions. It can be efficient in terms of programme and capital cost but recently also in terms of sustainable development with minimal waste due to the close control of factory conditions.
Consulting engineers are engaged in projects developed through modular construction methods routinely. There may be a requirement to provide design services for any or all of the following reasons –
- Design of the individual modular unit frames,
- Overall building stability and robustness design,
- Design of foundations
- External pavement and civil engineering design
ORS has recently been engaged in several projects where some combination of these services have been provided. Close collaboration is always required between the consulting engineer and modular unit manufacturer to ensure design decisions are communicated and also to provide a robust overall certification strategy in terms of BC(A)R certification. Communication of load-paths at an early stage will feed into specialist items such as site investigation procurement.
In terms of foundation design, a practical design and construction sequence must be put in place to allow for support as required by the frames and allow for the free servicing of the units in the void space below each unit. Figure 1 provides gives two such design approaches, with one consisting of blockwork piers cast onto concrete strip footings and the other consisting of concrete pads poured on a uniform layer of compacted granular fill. Both approaches have their merits, driven by both the main contractor and modular unit supplier.
Regarding structural design above ground level, modular units themselves require lateral and vertical stability assessment. Units are typically designed with mild steel corner posts and pressed metal floor and roof joists with timber skins providing lateral stability. With increasing numbers of modules and storeys, mild steel bracing is often introduced. Finally, while consulting engineers consider the robustness of unit connections for all buildings, this becomes increasingly important for buildings with consequence class 2B and above where vertical tie requirements are imposed to prevent disproportionate collapse should a failure occur. This includes many building forms up to 15 storeys in height and in the case of residential buildings, greater than four storeys.
Site construction programmes are extremely efficient with modular construction due to the amount of off-site fabrication. An image taken during delivery and installation for a primary school development is given in Figure 2 which shows the three-dimensional modules being lifted onto foundation pads.
ORS is engaged on several projects to provide Civil & Structural Engineering design to clients developing modular buildings, with services tailored to suit client and contractor needs.
Contact our ORS team today at info@ors.ie.